
How are you going to print one thing bigger than the printer itself? That’s the issue researchers Xu Zhang, Mingyang Li, Quang-Cuong Pham, and others got down to resolve on the Singapore Centre for 3D Printing at Nanyang Technological College (NTU).
Their answer: mounting the 3D printers on a pair of Ridgeback cell robots, who work collectively to print completely different sections of the identical half.
Impressively, the robots work on the similar time and in overlapping workspaces. In truth, the paper, revealed in August 2018, marks the primary time a big concrete construction has ever been 3D-printed by a number of robots concurrently!
3D printers go cell
Most 3D printing methods lack scalability:
- Gantry-based methods—by which a cartesian robotic strikes inside a cage—are giant and inefficient. To print a meter-long construction, for example, you’d want a cage of not less than 1 meter cubed. This large exterior framework means you’ll be able to’t construct something greater than your system.
- Robotic-arm-based printers are considerably extra environment friendly than gantries, however they nonetheless take a very long time to print something, as a result of a single print nozzle nonetheless hogs your complete print area.
- Multi-robot methods like Minibuilders will not be ultimate for printing concrete buildings, as a result of the primary layer of concrete must harden earlier than the climbing robots can proceed to print the following part.
As you’ll be able to see, mounting 3D print nozzles on robotic arms is nothing new. What’s completely different right here is that the researchers mounted the arm itself on a cell base—permitting the print nozzle to maneuver round in an even bigger workspace—and so they discovered how one can get two robots to construct a construction on the similar time.
The result’s a scalable system: one which lets the consumer introduce as many robots as wanted to finish a printing job rapidly and effectively.
The staff began with a 3D simulation of the Ridgeback-based robots, planning the “nozzle path” of the construction they needed to print.
Picture supply: NTU Singapore
The way it all works
The staff began with 3D fashions of every {hardware} part (offered by the producers). Working inside a CAD program, they deliberate the “nozzle path” for the construction they needed to print. This was basically simply slicing the specified construction into layers, every of which represented a path that the robotic arm would comply with.
Subsequent, they allotted the robots to explicit sections of the construction. On this case, every robotic was liable for printing half of the construction.
Then they deliberate the robots’ motions, taking care to keep away from collisions. This was an iterative course of: the staff needed to create a movement plan, run a simulation, establish any collisions, repair the plan, re-run the simulation…
Lastly, they set the robots unfastened to print the construction (see video under).
You would possibly discover a man holding a educate pendant within the background. He’s not controlling the robots—as soon as the robots have been programmed, the constructing course of is fully autonomous. He’s simply there to hit “cease” in case the robots go haywire and begin spraying cement on the partitions (which happily hasn’t occurred but).
Ridgeback leads staff to success
The staff used two Clearpath Ridgeback cell robots of their experiments. These indoor robotic platforms served as the bottom upon which the robotic arm, controller, sensors, pump system, and print nozzle had been mounted.
As Quang-Cuong Pham, Assistant Professor of Mechanical and Aerospace Engineering at NTU, says, “The Ridgeback was an excellent alternative for us due to its excessive payload capability. Different cell platforms merely wouldn’t meet the calls for of the job.”
He explains, “Our robotic arm weighed 50 kg, and with the nozzle, controller, and all the remainder of it on prime of that we had been including 70 kg complete to every platform. Happily the Ridgeback has a 100 kg payload, so we didn’t have to fret about overloading it.”
The excessive payload capability wasn’t the one profit. The staff additionally preferred how the Ridgeback has holonomic drive, with 4 independently pushed, omni-directional wheels.
Typical robots-on-wheels are non-holonomic: they’ll solely transfer backwards and forwards, not side-to-side. The Ridgeback, in contrast, can transfer in all instructions. This makes it a lot simpler to maneuver in exact paths.
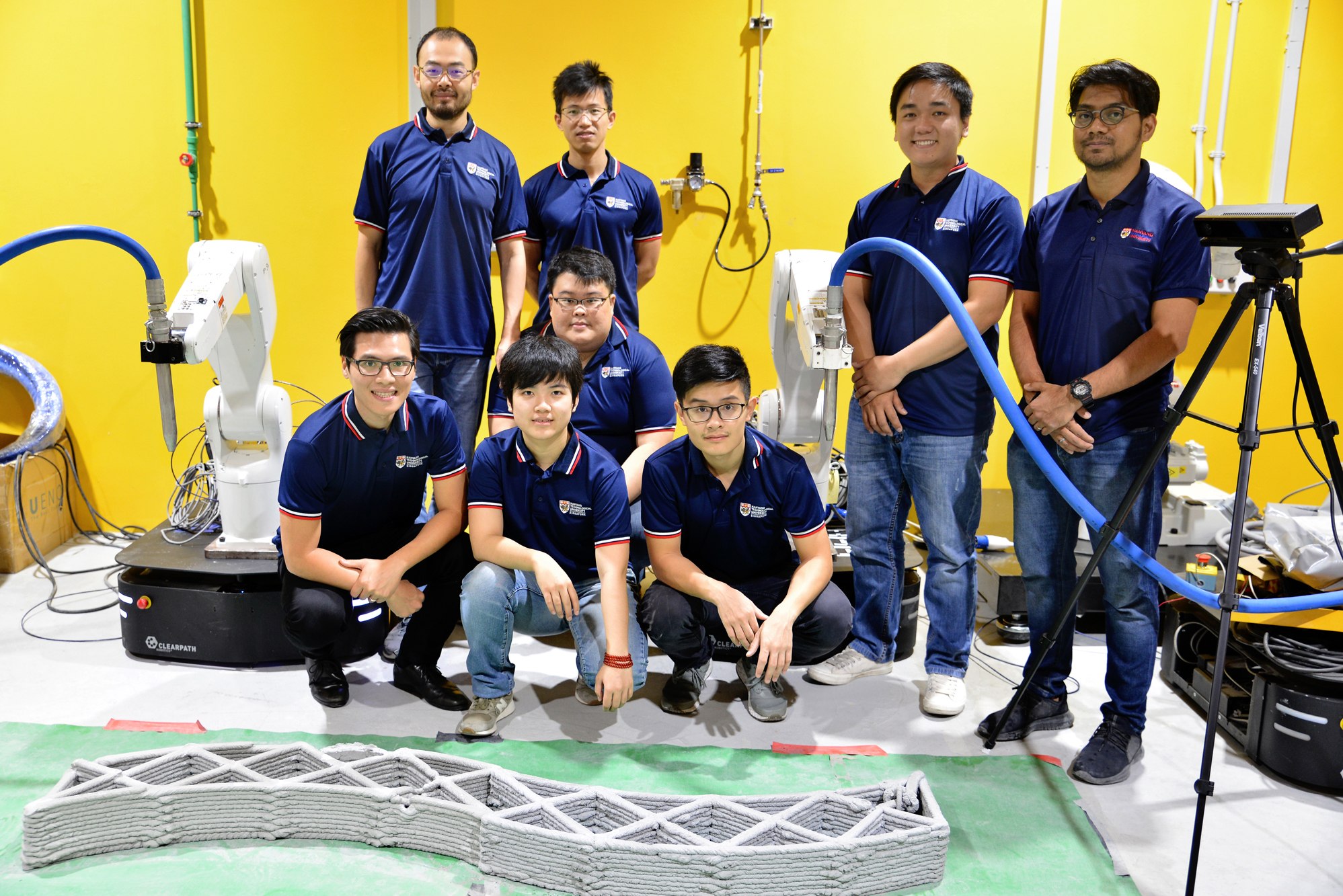
Picture supply: NTU Singapore
What’s Subsequent?
After publishing this paper, the staff needed to take their cell printing system to the following stage—by constructing one that would print whereas shifting. They wasted no time, discovering an answer inside just some months!
To date on this weblog submit, we’ve been discussing a system the place the platform stays immobile whereas the robotic arm prints the item. However within the staff’s newest methodology (detailed on this paper), the platform and printing arm transfer concurrently.
Test it out within the video under.
Why is that this such an enormous deal? As a result of it overcomes an enormous hurdle to printing greater buildings. With the previous stationary system, the robotic may solely print throughout the space its arm may attain. To construct greater buildings, you needed to put a number of robots to work alongside one another.
With the brand new system, although, this dimension restrict now not applies. For the reason that robotic can transfer round, you’ll be able to construct a lot greater buildings with only one robotic.
After all, there’s nonetheless quite a lot of work to do. The staff desires to combine extra sensors, discover higher part-joining methods, and develop a motion-planning answer for a number of printing-while-moving robots.
They usually gained’t cease there. In alignment with NASA’s 3D-Printed Habitat Problem, their final objective is to create robots that may construct autonomously in excessive environments—from essentially the most distant caves on Earth to the moon, Mars, and past.
Be taught extra
To study extra in regards to the Singapore Centre for 3D Printing, click on right here.
To study extra about Clearpath’s Ridgeback indoor robotic platform, click on right here.